- Home /
- Fobes India Blogs /
- the-innovation-edge /
- six-myths-surrounding-3d-printing-in-india
Six myths surrounding 3D printing in India
The technology has been in India for three decades now, but is not yet the answer to every manufacturing problem
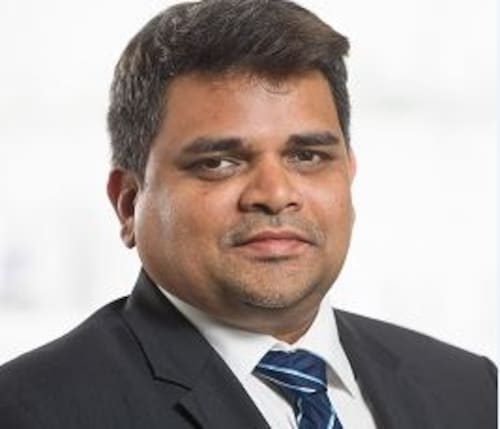
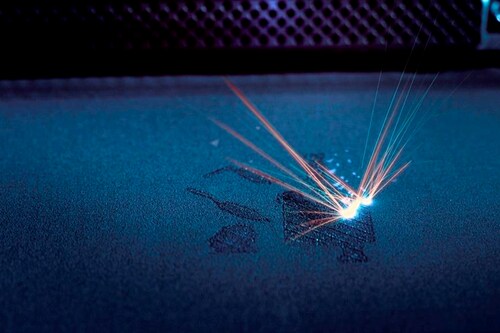
Though there are several misconceptions hounding additive manufacturing, both positive and negative, the following seem to stand out the most, as these have impacted the growth of AM in India.
Myth 1: No design limitation
A very popular phrase within the manufacturing industry is that “complexity is free” when you adapt the additive manufacturing process. What this means is that when you employ the AM process in your manufacturing plant, you can create the most complex designs easily. Now, it is true that additive manufacturing makes room for complexity in design of several components; however it still does have certain design limitations. To begin with, when we talk about creating a design for manufacturing, there must be some design rules that need to be kept under consideration.
A very popular phrase within the manufacturing industry is that “complexity is free” when you adapt the additive manufacturing process. What this means is that when you employ the AM process in your manufacturing plant, you can create the most complex designs easily. Now, it is true that additive manufacturing makes room for complexity in design of several components; however it still does have certain design limitations. To begin with, when we talk about creating a design for manufacturing, there must be some design rules that need to be kept under consideration.
Some components with intricate designs, such as ones having thin walls, will require support structures to maintain the integrity of the structure until post-processing. In post-processing, the techniques employed for each component will be dependent on the size, structure and even the alloy used to build it.
Myth 2: Additive Manufacturing is expensive
This purely depends on its use case. What is AM being used to produce? Keeping in mind that customisation always has its costs involved, understand that AM is not here to replace the traditional manufacturing process. It does not have solutions to all manufacturing challenges. But, it does offer faster lead time, better cost, and overall better production option, for many existing manufacturing needs.
This purely depends on its use case. What is AM being used to produce? Keeping in mind that customisation always has its costs involved, understand that AM is not here to replace the traditional manufacturing process. It does not have solutions to all manufacturing challenges. But, it does offer faster lead time, better cost, and overall better production option, for many existing manufacturing needs.
Myth 3: Zero wastage with Additive Manufacturing
When it comes to efficient use of raw material, additive manufacturing does have its advantages. However, this does not mean that there is zero wastage. Although 3D printing mostly works on the principle of curing a single layer at a time while building a component, there still is some minimal amount of wastage. The raw material can be re-used after going through a sieving process and mixing with new powder. Hence, it is far more viable to reuse alloys in additive manufacturing as the integrity of the element isn’t hampered too much by the whole process.
When it comes to efficient use of raw material, additive manufacturing does have its advantages. However, this does not mean that there is zero wastage. Although 3D printing mostly works on the principle of curing a single layer at a time while building a component, there still is some minimal amount of wastage. The raw material can be re-used after going through a sieving process and mixing with new powder. Hence, it is far more viable to reuse alloys in additive manufacturing as the integrity of the element isn’t hampered too much by the whole process.
Myth 4: 3D printing is for small components with no need of assembly
It does hold its advantages in creating smaller intricate parts with impressive quality, most of the time being highly cost-effective too. But, when we talk about industries like aerospace and automotive, many larger components are also being built using the AM process. Developing aircraft components has always been an expensive affair with long lead times. To add to the misconception, it is generally believed that 3D printing of components allows one to make a single solid block. It is highly unlikely that assembly of multiple components can be reduced to nil. There is a definite scope for reduction in number of components that make up a complete unit, if it satisfies certain engineering criteria. If we think about it, even this minimal reduction was unheard of a while ago. Making AM a viable alternative in manufacturing quality components.
It does hold its advantages in creating smaller intricate parts with impressive quality, most of the time being highly cost-effective too. But, when we talk about industries like aerospace and automotive, many larger components are also being built using the AM process. Developing aircraft components has always been an expensive affair with long lead times. To add to the misconception, it is generally believed that 3D printing of components allows one to make a single solid block. It is highly unlikely that assembly of multiple components can be reduced to nil. There is a definite scope for reduction in number of components that make up a complete unit, if it satisfies certain engineering criteria. If we think about it, even this minimal reduction was unheard of a while ago. Making AM a viable alternative in manufacturing quality components.
Myth 5: Additive Manufacturing is for everyone
It is necessary for organisations to identify the scope of AM technology with respect to their needs, and figure out whether this can be built in house or if it needs to be outsourced.
It is necessary for organisations to identify the scope of AM technology with respect to their needs, and figure out whether this can be built in house or if it needs to be outsourced.
Myth 6: Additive Manufacturing is a brand-new technology
Popularly generalised as 3D printing in media, additive manufacturing was first introduced in the early 80s. Ever since, it has seen wide usage. The number of materials that can be used has grown two-fold every couple of years. Like every innovation, additive manufacturing has also gone through a cycle of constant upgrade and with decades of research and successful implementation, it has reached a commendable pinnacle in the manufacturing field.
Popularly generalised as 3D printing in media, additive manufacturing was first introduced in the early 80s. Ever since, it has seen wide usage. The number of materials that can be used has grown two-fold every couple of years. Like every innovation, additive manufacturing has also gone through a cycle of constant upgrade and with decades of research and successful implementation, it has reached a commendable pinnacle in the manufacturing field.
Conclusion
In India, with organisations like ISRO using AM to create their rocket components, speaks volumes of the reliability of additive manufacturing. Some support from the government to bring this technology to the fore would speed up the adoption of this technique within the country, in congruence to its global growth.
In India, with organisations like ISRO using AM to create their rocket components, speaks volumes of the reliability of additive manufacturing. Some support from the government to bring this technology to the fore would speed up the adoption of this technique within the country, in congruence to its global growth.
The writer is Regional Manager at EOS India.
Popular Now
- Shifting Trade Ties: India's FTA Strategy Moves West
- From constraints to commerce: Transforming women-led businesses in India through
- India's semiconductor boom hinges on ecosystem growth
- AI, humans and India's role in this tech revolution
- Budget 2025: A new dawn for the middle class and a prosperous future
- Budget 2025 expectations in a protectionist world
- WEF 2025 Wrap-Up: Unlocking the Intelligent Age through collaboration, transform
- Leveraging waste-to-energy innovation for India's legacy waste crisis
- Is the quiet evolution of a new normal growing up with humans and AI?
- Insurance for all by 2047 A push for awareness, accessibility, & affordability