Covid-19 pushes 3D printing to new dimension
The unorganised and sluggish 3D printing sector could have a windfall gain as companies make PPE and other critical equipment to fight the Covid-19 crisis
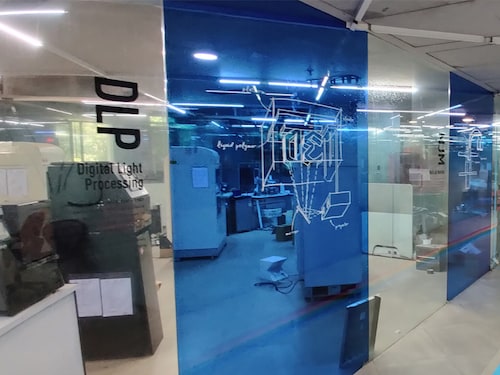
Imaginarium, a Mumbai-based boutique 3D printing firm, whose focus has been on jewellery, furniture and medical implants, is now racing to make PPE face shields and 3D-printed circuit splitters that will allow multiple patients to use a single ventilator
A few days before Prime Minister Narendra Modi announced the first nationwide lockdown to control the spread of the coronavirus on March 24, an intern at Boson Machines, an additive manufacturing startup based in Mumbai, pitched an idea: With the situation getting worse, could 3D printing help?
Until now, the company’s focus has been on manufacturing the 3D printing machines themselves. Overnight, they found an open source design and printed a sample of a plastic face mask, similar in design to the N95 that is in great demand at the moment. “That’s what lit the spark,” says Arjun Panchal, 25, who co-founded Boson Machines with his brother, Parth, 27. “The next day, I saw a tweet from a doctor in Bengaluru saying there’s a huge requirement for certain products. We immediately set things in motion.”
The Panchal brothers consulted with physician Dr Swapneil Parikh, who has co-authored a book called The Coronavirus: What you Need to Know about the Global Pandemic. Parikh has helped Boson Machines develop its core products in response to the Covid-19 crisis: Medical grade face shields made of PVC, with an elastic polycarbonate headband that has foam cushioning.
Face shields are considered an integral part of the PPE (personal protective equipment) for health care workers, adding a layer over the face mask and protecting the wearer from any contaminated droplets they may encounter.
Boson has delivered more than 12,000 face shields since, to hospitals including Jaslok, Kasturba, KEM and Cooper in Mumbai. “Four days ago, our capacity was to produce 800 pieces per day. But now, with the help of the Maharashtra government, we can make 6,000 masks a day,” says Arjun.
The project is entirely crowdfunded—the duo raised close to ₹21 lakh in five days ending March 30 on crowdfunding platform Ketto, after running a campaign with social media celebrity Kusha Kapila. The state government asked them to amplify production, and fast-tracked all permissions needed. Boson has now developed a network of about 150 3D printing machines, so the face shields are being printed at factories from Vasai to Colaba, then brought to their headquarters in Goregaon for the final assembly and quality checks.
Like Boson, many startups with access to 3D printing facilities have stepped up to help provide health care equipment across the country, using inventive designs—and developing entirely new business models in the process too.
For instance, Bengaluru-based Harkness Screens, a 90-year-old company that makes cinema screens for the country’s leading multiplexes, has now taken to 3D printing face shields, along with PVC aprons and curtains for doctors and quarantine centres, which can be sprayed with sanitiser and quickly disinfected.
(From left) Parth and Arjun Panchal of Boson Machines make 3D printers, but are now working with hospitals to make face shields, valves for oxygen masks and plastic masks
Mumbai’s Imaginarium, whose core business is 3D-printed jewellery, has all hands on deck to make face shields too. Imaginarium is also attempting to produce circuit splitters for ventilators, so multiple patients can use the same ventilator—as is Bengaluru-based Ethereal Machines, a deep tech startup that builds CNC (computer numerical control) machines, hardware and software, which control processes such as 3D printing.
“I’m a motorcyclist and I’ve always been fascinated by the story of Ducati, which started off making radio equipment until after their factory was bombed in the Second World War,” says Preetham Daniel, senior vice president - Asia, Harkness Screens. “BMW began as a jet engine maker. I’m always fascinated by such stories, and consciously keep them in mind. To me, this situation is nothing less than a war. Companies will need to adapt. Who knows, our future might be in medical grade equipment.”
Daniel says he and his company had no prior experience in the field—“I didn’t even know what a face shield was, I was calling it a visor,” he laughs—but they could leverage their expertise in dealing with the PVC fabric, which is also used in their cinema screens.
While they started with an open source design, they had to tweak it to suit local needs. “Open source designs are a great start point but they are very generic,” he says. “For example, it’s common in India to have longer hair—in the original design, if the doctor had a braid tied, the headband would just slip off. We had to make the back protected such that it would stay in place under any condition.”
They have produced 4,000 each of face shields and curtains, and should have a total of 25,000 face shield orders fulfilled by the end of the month, hoping to escalate to 1,50,000 in the next order batch. Two thousand aprons will be delivered after restrictions are lifted.
(From left) Kaushik Mudda and Navin Jain of Bengaluru-based Ethereal Machines are making parts for ventilator splitters
Battle to breathe
India is estimated to have 40,000 ventilators, of which about 20 to 25 percent could be dysfunctional that leaves about 30,000 to 32,000. In a worst-case scenario, India will need between 1.1 lakh and 2.2 lakh ventilators by mid-May, says a study from US-based think tank Brookings Institution.
“If people don’t stay home and we can’t control this, we’re in deep trouble,” says Kaushik Mudda, co-founder of Ethereal Machines, which raised $1.25 million last year from investors including Bloom Ventures, Citrus Pay founder Jitendra Gupta and others. “It could take about three months to make so many ventilators and those that companies like Mahindra are putting their might behind are essential war solutions, but not the complex ventilators we need to really get the job done. We started thinking about what the next best thing was to augment ventilator capacity.”
Ethereal started working on their solution on the day PM Modi announced the first phase of the nationwide lockdown. “It’s been crazy,” Mudda says. “The first five days, we were just driving around from hospital to office, without permits, braving it out, hoping that if somebody stopped us, we would explain to them what we were doing and they would let us go.”
In the second week, they got permission from government authorities to make ventilator equipment. “We decided to put our deep tech expertise to use,” he adds.
As the crisis played out in Italy, when doctors had to pick and choose between patients, the idea of a 3D-printed splitter came to the fore—where an extra attachment is built for the outside of the ventilator, where the oxygen supply goes from. It splits the supply 50:50 amidst two patients.
“It’s an extreme, last-resort measure,” cautions Mudda. “When we started talking to doctors here, we realised that the issue on ground is with that 50:50 ratio. Different patients have different requirements, and the equal split often ends up making one patient collapse faster while the other recovers. The actual split required could be 30:70 or 40:60, depending on the health of each patient.”
The other issue is of cross-contamination of previous, other illnesses between the patients. Mudda and his team began working on ‘differential ventilation’ that can also prevent cross-flow and claims to have cracked it for the first time in the world. “We were no experts in ventilators or pulmonology, but we sat with doctors to understand how ventilators work. It took us eight iterations over 10 days to perfect a prototype. That speed is thanks to 3D printing.”
Across the world, 3D printing is being used for quick prototyping. It doesn’t need expensive, cumbersome mould making, and lets you print minimal quantities and modify designs down to details. All you need to do is then download the design and procure the material needed.
“3D printing immediately puts out results, and time is absolutely essential right now,” Mudda adds. “We’ve finalised on a design and as we speak, it’s being tried on a test lung. But this is one of those few times when I’m hoping someone doesn’t have to use what I create—it’s really an extreme, last-case measure.”
The 3D printing technology also enabled Inali, a non-profit in the assistive health care field, to quickly iterate a smart ventilator design. Inali, which works between Vadodara and Pune, has been making affordable prosthetic arms for certain upper limb disabilities since 2015. It uses 3D printing extensively to create prototypes. The company’s founder and CEO Prashant Gade, through a course in Paris, has found mentorship in multinational software firm Dassault Systèmes, which specialises in 3D software and engineering.
As part of Dassault’s open innovation and startup accelerator programme, the 3DExperience Lab, Inali began work on a rapid prototyping system in early April. “With permissions in place, we can create 100 ventilators in 15 days,” says Gade. “3D printing lets us use simulation and modelling to see how the system will actually behave, without rigorous trials needed. We’ve got permission from local authorities to travel for material and research, and have built our prototype.”
Inali’s ventilator automatically measures pressure—giving a patient extra pressure could kill him or her—detects leakage and volumes, among other parameters that WHO recommends for monitoring coronavirus patients. The prototype is pending medical approval with government authorities at the time of writing.
Preetham Daniel"s Harkness Screens usually manufactures cinema screens, but since the crisis began it has pivoted to making face shields and aprons using 3D printers
Turning point?
The full potential of 3D printing is yet to be seen in India, where adoption has been largely fragmented. According to a 2018 report by Wohlers Associates, a 3D printing market research firm, India makes up 3 percent of total 3D printing units in the Asia-Pacific region, while China and Japan hold 35 percent and 30 percent respectively.
One of the factors is the prohibitive cost of the machines themselves—the most basic 3D printer variants can cost between ₹2 lakh and ₹5 lakh. The second factor is time while the technology is great for rapid prototyping, it is slow to mass produce.
It takes six to eight hours to make one unit of the ventilator splitter, explains Mudda of Ethereal Machines, and about 1.5 hours to create a single face shield, says Panchal of Boson Machines.
“Unless you have a whole line of 3D printers continuously working, you can’t get into the volumes required to address this immediate crisis,” adds Daniel. “In a normal situation, it would have been fine. But right now, demand is running into thousands a day. Even at about 35 minutes a piece, it really takes a toll on the machine.”
Most startups, then—besides Boson, which has enlisted a wide network of printers that are constantly running—are limiting the use of 3D printing to the prototyping stage. Conventional processes like injection moulding, instead, prove more cost effective and efficient to mass produce.
“We went from dumbphones to smartphones in just about two or three years,” says Imaginarium founder Guruprasad Rao. “But even after 30 years of existence, 3D printing has not commanded that kind of disruption.”
One of the main problems, Rao adds, is that there is no concept of economies of scale in 3D printing. Even in mass production, it could cost about three times as much to produce a single 3D printed face shield (Harkness estimates this cost at about ₹65), versus that of injection moulding (in which cost could come down to as low as ₹20 per piece).
“However, we choose to leverage the technology’s strengths instead. So as a company, we work on making one-of-a-kind jewellery pieces, or patient-specific implants. For example, every person’s skull is different. If someone has an accident, their skull will need a uniquely shaped implant, and that kind of custom build with biocompatible or implantable material is made possible by 3D printing.”
In crises like the current pandemic, such strengths could outweigh the technology’s weaknesses. “Certainly, the global pandemic has given a tremendous boost to the 3D printing industry,” says Bhavesh Kumar, SIMULIA lead, India, Dassault Systemes. “However, if we have to make 3D printing successful in India, we first need to build a strong foundation of know-how. In post-Covid India, we should see companies exploring how 3D printing can cater to local demand that was not considered earlier. It is also important to identify the right demand in the market, connect with the right stakeholders and respond expeditiously.”
Currently, when logistics are proving to be a huge challenge because of the lockdown, 3D printing could help fix the critical supply gap of PPE and medical equipment. “Even if I have the capacity to produce 30,000 units, I might not be able to distribute them to where they are needed,” adds Mudda. “Meanwhile, if someone in, say, Kolkata, can download my design, print and hand it over to a local hospital, it might help save lives.”